
The Future of Plant Tissue Culture: Inside the Rise of Automation and Robotics
As a content and community manager, I leverage my expertise in plant biotechnology, passion for tissue culture, and writing skills to create compelling articles, simplifying intricate scientific concepts, and address your inquiries. As a dedicated science communicator, I strive to spark curiosity and foster a love for science in my audience.
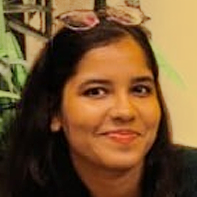

Introduction
The integration of automation, robotics, and the analytical power of artificial intelligence (AI) is set to revolutionize plant tissue culture, transforming it from a specialized, craft-based technique into a high-efficiency, industrial-scale operation.
Plant tissue culture (PTC)—it sounds like something straight out of a sci-fi novel, doesn't it? Yet, this incredible scientific discipline, the art and science of growing plants from just tiny pieces of tissue or even single cells in a sterile laboratory setting, has been a quiet cornerstone of plant biotechnology for decades. Its power lies in its ability to rapidly multiply elite plant varieties, produce plants free from diseases, and even help conserve rare and endangered species.
For years, however, the promise of PTC has been somewhat tethered by its very nature: it's incredibly labor-intensive, requiring meticulous, repetitive manual work by skilled technicians. This human element translates to high operational costs and significant challenges when trying to scale up to meet the ever-increasing global demands for food, forestry products, and ornamental plants.
But imagine a PTC lab where the hum of sophisticated machinery and the precise, tireless movements of robotic arms are as common as the sight of Petri dishes. This isn't a distant dream; it's the rapidly unfolding present.
Rise of the Robo-Botanists: Precision and Pace Unleashed

The most immediate and visible transformation in modern PTC labs is the deployment of robotic systems. These are not your clunky, all-purpose factory robots, but highly specialized machines designed for the delicate and repetitive tasks that define much of tissue culture work.
One of the most labor-intensive areas traditionally has been the preparation and handling of explants – the tiny pieces of plant tissue used to initiate cultures. Robots are now stepping in to:
-
Automate Explant Preparation and Transfer: Systems are being developed to precisely cut plant material into explants of desired sizes and then accurately transfer them to nutrient media. This might involve robotic arms with fine scalpels or even non-contact methods like lasers for dissection.
Subculturing, the vital process of moving growing tissues to fresh media, is also a prime candidate for robotic automation. For instance, NuPlant's SmartClone™ system employs robotics for these tasks, often using unique "plantlet pods" that simplify robotic handling and allow for environmental adjustments around the developing plantlet.
-
Enhance Sorting and Quality Control: When combined with machine vision, robots can inspect, sort, and grade plantlets based on predefined quality parameters like size, shape, color, and overall vigor, far surpassing the speed and consistency of human visual inspection.
The RoBoCut system, for example, uses AI-guided 3D image recognition to direct a laser for hygienic cutting and sorting, reportedly reducing plantlet failure rates and production costs. Viscon Plant Technology also offers sophisticated selection and grading machines using advanced vision software.
-
Streamline Harvesting: Even the process of moving mature plantlets from the sterile lab environment to ex vitro conditions for acclimatization is being automated. NuPlant’s Janus Transplanter, for example, can take culture pods and automatically transfer the agar plugs containing plantlets into nursery trays.
The impact of these robotic assistants is multi-faceted. They promise significantly increased throughput, with some systems capable of processing thousands of plantlets per shift. This leads to greater efficiency and a dramatic reduction in labor costs, which can traditionally account for a staggering 50-70% of the total production cost in micropropagation. Moreover, the precision of robotic operations enhances the consistency and quality of plantlets and significantly minimizes the ever-present risk of microbial contamination that can arise from manual handling.
Beyond Dexterous Digits: Crafting Intelligent Growth Sanctuaries

Automation in PTC isn't just about robotic arms performing physical tasks; it's also about creating highly controlled and optimized environments for plant growth. This is where automated incubation systems and advanced bioreactors come into play.
Traditional growth rooms often have limitations in maintaining perfectly uniform conditions. Automated incubators and dedicated plant growth chambers are changing this by offering precise, dynamic control over a suite of crucial environmental factors. Imagine being able to meticulously regulate:
-
Temperature (often with programmable day/night differences)
-
Light (intensity, spectral quality, and photoperiod, increasingly using LEDs)
-
Relative humidity (often kept high to prevent desiccation)
-
CO2 concentration (especially vital for photoautotrophic cultures)
-
Air circulation
This level of control, often managed by sophisticated systems like the Certhon Control System (CCS), helps to create the ideal microenvironment for specific plant species or developmental stages, minimizing stress and maximizing growth.
For large-scale propagation, particularly when using liquid media, bioreactor technology represents a monumental leap.
Among these, Temporary Immersion Systems (TIS) have gained significant traction. Instead of continuous submersion, TIS periodically floods the plant material with a liquid nutrient medium and then drains it away. This clever design helps to:
-
Improve nutrient uptake.
-
Reduce problems like asphyxia (oxygen deprivation).
-
Minimize hyperhydricity (a physiological disorder causing water-logged tissues).
-
Allow for easier automation of media exchange. Systems like the RITA® bioreactor and PCT's BioCoupler™ with BioTilt™ exemplify this approach, leading to increased biological yield, reduced labor, and often, more robust plantlets that acclimatize better to greenhouse conditions.

Another innovative approach is Photoautotrophic Micropropagation (PAM), where plantlets are grown on sugar-free media, relying entirely on photosynthesis for their energy. This can produce stronger plantlets and reduce contamination risks associated with sugar-rich media.
Underpinning these smart environments is an array of advanced sensors that continuously monitor everything from temperature and humidity to CO2 levels and even pH within the culture medium. This real-time data is invaluable for fine-tuning conditions and ensuring optimal growth.
The "Brain" of the Operation: AI and Machine Learning Take the Helm
If robotics provides the brawn and sensors the senses, then Artificial Intelligence (AI) and Machine Learning (ML) undoubtedly represent the evolving "brain" of the automated PTC laboratory. These computational powerhouses are shifting PTC from a practice often reliant on empirical knowledge and trial-and-error towards a more predictive, precise, and data-driven science.
How is AI making its mark?
-
Predicting Optimal Conditions: One of the biggest time sinks in PTC is figuring out the perfect growth recipe for a new plant species or variety. AI algorithms (like Artificial Neural Networks, Support Vector Machines, and Decision Trees) can analyze vast datasets from previous experiments to predict the ideal sterilizing agent concentrations, media formulations (including plant growth regulators), and environmental parameters (temperature, light, etc.). This can dramatically shorten protocol development time.
-
Managing Developmental Stages: AI models are being trained to optimize each critical phase of in vitro growth, including callogenesis, somatic embryogenesis, shoot and root development, and even the challenging acclimatization stage. For example, AI can help determine the optimal timing for subculturing to maintain plantlet vigor.
-
Automated Image Analysis: AI-driven machine vision is becoming an invaluable tool for non-invasively monitoring cultures. Systems can automatically capture images and use AI to assess growth rates, identify morphological characteristics, detect early signs of contamination or stress (like vitrification), and perform quality control checks with a level of objectivity and consistency that humans struggle to match.
The sheer volume of data generated by automated systems—from environmental sensors, imaging platforms, and robotic operations—provides a rich playground for AI and ML to drive continuous process optimization and lead to more adaptive and resilient production systems.

Towards the Fully Automated Lab: Integrated Platforms and Data Ecosystems
The evolution of automation in PTC is not just about automating individual steps in isolation. The real power emerges when these technologies are woven together into integrated platforms that can manage entire workflows, all underpinned by robust data management systems.
Imagine a laboratory where:
-
Media is automatically prepared and dispensed by systems like RAYPA's AE-MP Series.
-
Robots handle the precise cutting and transfer of explants.
-
Cultures are moved into and out of automated incubators like those offered by Automata, which maintain optimal conditions and minimize human interference.
-
Machine vision systems continuously monitor growth and quality.
-
All data, from environmental parameters to growth metrics and processing steps, is captured and managed by Laboratory Information Management Systems (LIMS) or specialized tracking software like 2nd Sight's TCTrak or Viscon's Factory Intelligence.
This integration allows for seamless workflows, enhanced traceability, and the creation of rich datasets that are vital for AI-driven optimization and decision-making. Companies like Viscon Plant Technology are offering such comprehensive turnkey solutions, including facility design, climate-controlled propagation rooms, and integrated software.
Navigating the Bumps on the Automated Road
While the vision of a fully automated, intelligent PTC lab is incredibly exciting, the path isn't entirely smooth. There are significant hurdles to overcome:
Technical Challenges:
-
System Integration & Interoperability: Getting different automated systems from various vendors to work together harmoniously is a major task, requiring significant technical expertise.
-
Reliability, Maintenance, and Sterility: Complex robotic systems need regular maintenance, and ensuring the sterility of equipment that interacts with cultures is paramount and can be tricky.
-
Robotic Dexterity: Replicating the delicate touch and adaptive judgment of a seasoned human technician, especially when dealing with fragile and morphologically diverse plant material, remains a significant engineering feat.

Biological Challenges:
-
Plant Variability: Unlike standardized industrial parts, plant tissues are inherently variable in size, shape, and developmental stage, posing a challenge for rigid automation.
-
Contamination Risks: While automation reduces human-introduced contamination, large-scale systems, especially those with liquid cultures, can present new sterility challenges.
-
Genetic Stability: The stress of in vitro culture can sometimes induce undesirable genetic changes (somaclonal variation), a concern that automation doesn't inherently solve.
Economic and Operational Challenges:
-
High Initial Investment: The cost of acquiring sophisticated robotic systems, and software, and potentially renovating lab spaces is a major barrier, especially for smaller operations or those in developing countries.
-
Need for Skilled Personnel: Automation reduces manual labor but creates a demand for a workforce with expertise in robotics, AI, engineering, and data analysis, alongside plant science knowledge.
What do you think is the biggest hurdle for widespread automation in plant tissue culture today? Is it the cost, the technology itself, or something else?
The Horizon: What's Next for Automated Plant Propagation?
The journey of automation in plant tissue culture is far from over; in fact, we're likely just scratching the surface of its potential. Here’s a glimpse of what the future might hold:
Smarter, More Sensitive Systems: We can anticipate the arrival of next-generation robotic systems that are not only faster and more precise but also significantly more dexterous and capable of adapting to the inherent variability of biological materials.
Coupled with this will be increasingly sophisticated sensors. Imagine wearable sensors for plants that monitor stress indicators like hydrogen peroxide (H2O2) in real-time, or nanosensors detecting specific metabolites or pathogens directly within the culture vessel. This will allow for an unprecedented level of individualized care and monitoring.
AI-Driven Design and Dynamic Control: Artificial intelligence will become even more deeply embedded.
The goal is to move towards AI that can not only predict optimal growth conditions but also automatically design entire multi-stage culture protocols based on a plant's specific genotype and the desired outcome.
Think "computer-aided tissue culture design," where AI dynamically adjusts protocols based on real-time sensor feedback and culture performance.

Powerful Biotechnological Synergies: The true power will be unleashed through the integration of automated PTC with other revolutionary biotechnologies.
-
Genome Editing (e.g., CRISPR/Cas9): Automated PTC platforms are essential for efficiently regenerating whole plants from cells that have undergone precise genetic modifications. AI can help optimize the tissue culture stages specifically for these engineered cells.
-
Synthetic Biology: This can be used to design custom-tailored media components or even engineer novel metabolic pathways within cultured plant cells, with automated systems used for testing and scaling up. The FAST-PB pipeline at CABBI, integrating a biofoundry with robotics and synthetic biology, is a testament to this synergy.
The Vision of Autonomous "Bio-factories": The ultimate, albeit ambitious, goal for many in the field is the development of fully autonomous "bio-factories" or "plant factories".
These facilities would seamlessly integrate robotics, AI, advanced bioreactors, and sophisticated environmental controls to operate with minimal human intervention, achieving unparalleled levels of efficiency, consistency, and scalability in plant production.
Conclusion: Cultivating a High-Tech, Sustainable Future
The infusion of automation and robotics into plant tissue culture is more than just an upgrade; it's a paradigm shift. It's transforming a traditionally labor-intensive, costly, and scale-limited practice into a highly efficient, precise, and scalable powerhouse of plant propagation.
The journey toward universally adopted, fully automated PTC will undoubtedly involve overcoming challenges related to cost, technical complexity, and biological nuances.
However, the benefits are too compelling to ignore: significant reductions in labor costs, dramatic increases in the production of genetically uniform and disease-free plants, and enhanced quality and consistency.
These advancements are critical for bolstering global food security, supporting sustainable agricultural and forestry practices, and pushing the boundaries of plant science.
The future of plant tissue culture is bright, and it's increasingly automated. It’s a future where technology and biology work in concert, not just to grow plants, but to cultivate solutions for a more resilient and productive world. What an exciting time to be witnessing this green revolution!
Unlock the Future of Plant Cloning with Plant Cell Technology!
At Plant Cell Technology, we provide premium tissue culture solutions to help researchers, growers, and businesses achieve efficient, disease-free plant propagation at scale. From expertly formulated media to cutting-edge bioreactors and contamination control solutions, we’re here to support your success in tissue culture.
With decades of expertise, we’ve been at the forefront of advancing plant tissue culture by providing the tools, knowledge, and support needed to streamline propagation, reduce losses, and boost productivity. Whether you’re a commercial grower, research scientist, or an enthusiast exploring tissue culture, our products and guidance can help you achieve consistent and high-yield plant production.
Looking to optimize your lab processes and scale production?
Contact us today and take your plant cloning to the next level!
Blog Categories
View by Level
Popular Blogs
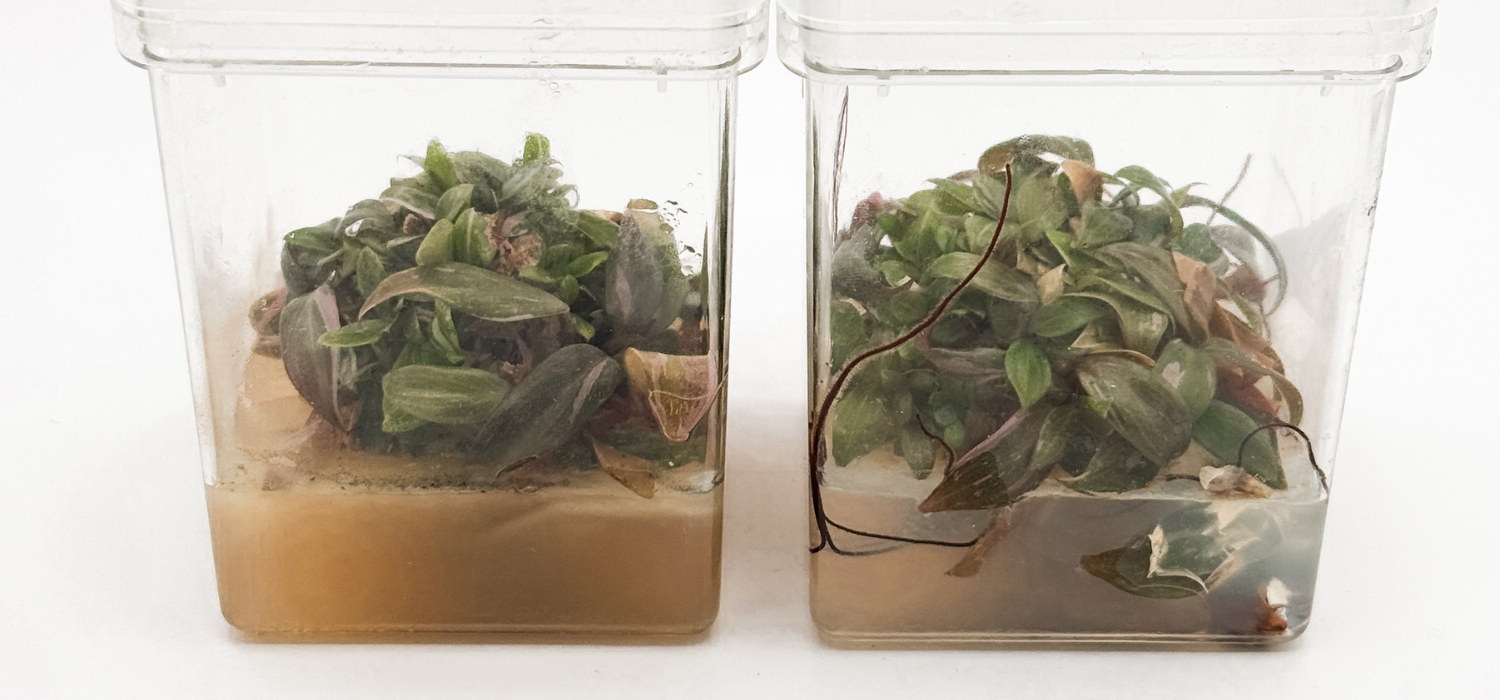
How to Troubleshoot Contamination and Browning in Plant Cultures
Introduction Plant tissue culture is a cornerstone of modern botany, enabling everything from the rapid propagation of elite crop varieties...
Read More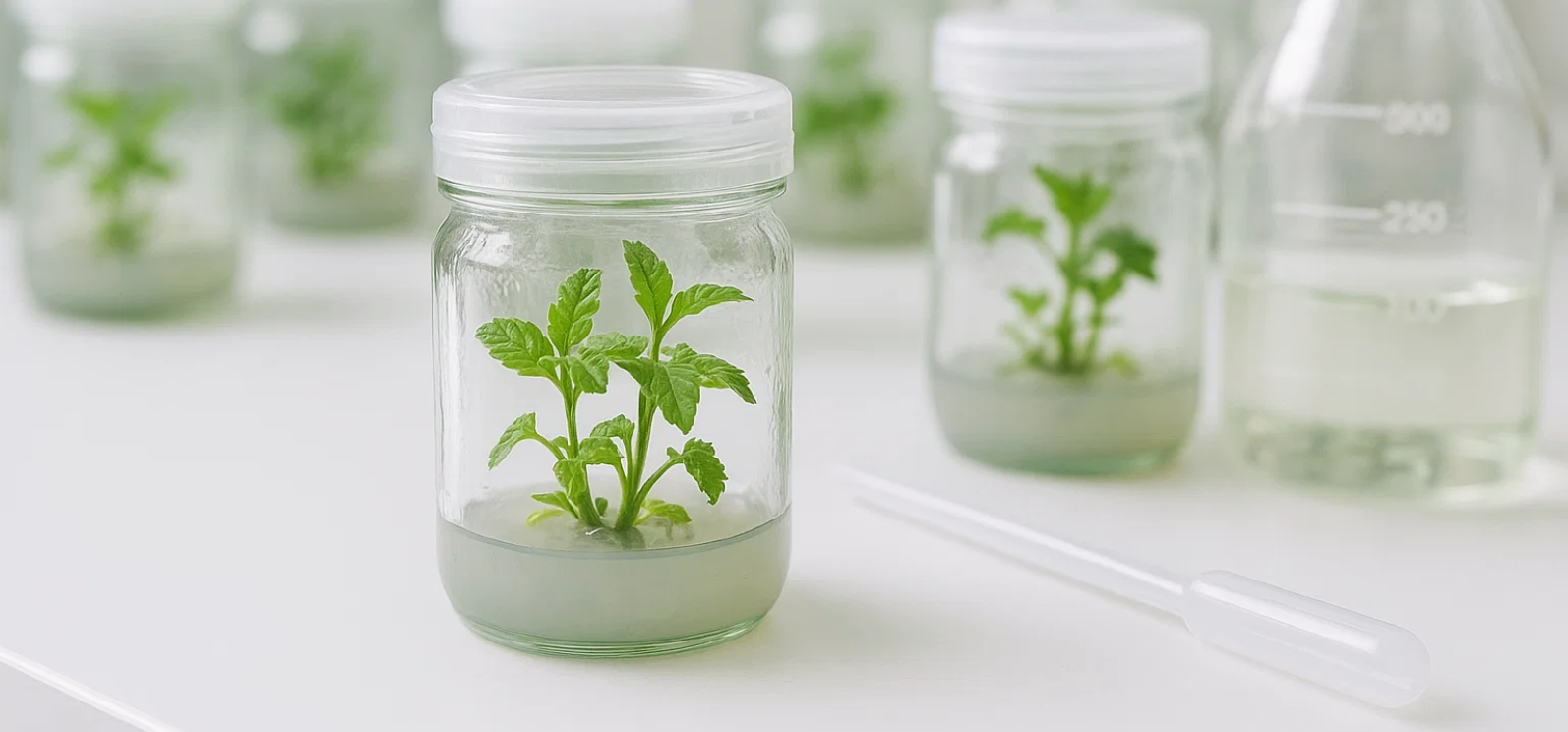
A Guide to Plant Growth: A Deep Dive into Tissue Culture Media
Introduction The ability to grow a complete plant from a small section of tissue is only possible through a scientific...
Read MoreSubscribe to Our Newsletter
Join the conversation
Your email address will not be published. Required fields are marked